2012年安全工程师《技术》复习资料:特种设备检测技术

特种设备检测技术
特种设备的种类、结构、类型繁多,其设计参数和使用条件各不相同,承压设备所盛装的介质可能具有不同程度的腐蚀或磨损的性质,因此,对它们进行检验时,必须采用各种不同的检验方法,才能对特种设备的安全使用性能作出全面、正确的评价。
(一)宏观检查
直观检查和量具检查通常称为宏观检查。宏观检查是对在用承压类特种设备进行内、外部检验常用的检验方法。宏观检查的方法简单易行,可以直接发现和检验容器内、外表面比较明显的缺陷,为进一步利用其他方法作详细的检验提供线索和依据。
1.直观检查
直观检查是承压类特种设备最基本的检验方法,通常在采用其他检验方法之前进行,是进一步检验的基础。它主要是凭借检验人员的感觉器官,对容器的内、外表面进行检查,以判别其是否有缺陷。
1)检查内容
直观检查,要求检查容器的本体和受压元件的结构是否合理,承压类特种设备的连接部位、焊缝、胀口、衬里等部位是否存在渗漏,承压类特种设备表面是否存在腐蚀的深坑或斑点、明显的裂纹、重皮折叠、磨损的沟槽、凹陷、鼓包等局部变形和过热的痕迹,焊缝是否有表面气孔、弧坑、咬边等缺陷,容器内、外壁的防腐层、保温层、耐火隔热层或衬里等是否完好等。
2)检查工具
用于直观检查的检查工具有手电筒、5—10倍放大镜、反光镜、内窥镜、约0.5 kg的尖头手锤等。
3)检查方法
(1)通常采用肉眼检查。肉眼能够迅速扫视大面积范围,并且能够察觉细微的颜色和结构的变化。
(2)当被检查的部位比较狭窄(例如长度较长的管壳式容器,以及气瓶等),无法直接观察时,可以利用反光镜或内窥镜伸入容器内进行检查。
(3)当怀疑设备表面有裂纹时,可用砂布将被检部位打磨干净,然后用浓度为10%的硝酸酒精溶液将其浸湿,擦净后用放大镜观察。
(4)对具有手孔或较大接管而人又无法进到内部用肉眼检查的小型设备,可将手从手孔或接管口伸入,触摸内表面,检查内壁是否光滑,有无凹坑、鼓包。
(5)用约0.5 kg的尖头手锤进行锤击检查是过去检查锅炉、压力容器的一种常用的方法。当容器表面有防腐层、保温层、耐火隔热层、衬里或夹套等妨碍检查时,如果需要应部分或全部拆除再进行直观检查。直观检查时,往往会在容器表面发现各种形态的缺陷,检验人员应予以综合判断,并分别予以适当的处置。
2.量具检查
采用简单的工具和量具对直观检查所发现的缺陷进行测量,以确定缺陷的严重程度,是直观检查的补充手段。
1)检查内容
用量具检查主要是检查设备表面腐蚀的面积和深度,变形程度,沟槽和裂纹的长度,以及设备本体和受压元件的结构尺寸(如容器的平直度、管板的不平度等)是否符合要求等。
2)检查工具
直尺、样板、游标卡尺、塞尺等。
3)检查方法
(1)用拉线或量具检查设备的结构尺寸。例如:用钢卷尺围出筒体的周长,用计算圆周长的公式和筒体的实际壁厚值算出筒体的平均内直径,以求得筒体的内径偏差;测量筒体同一断面的不圆度等。
(2)用平直尺紧靠设备、管板等的表面,用游标卡尺或塞尺检查设备的平直度,腐蚀、磨损、鼓包的深度(高度),管板的不平度等。
(3)用预先按受压元件的某部分做成的样板紧靠其表面,检查它们的形状、尺寸是否符合设计要求(例如角焊缝的焊脚高度、封头的曲率尺寸等),或测量其变形、腐蚀的程度。
(4)在器壁发生均匀腐蚀、片状腐蚀或密集斑点腐蚀的部位,目前通常采用超声波测厚仪测量容器的剩余壁厚。
(二)无损检测
在承压类特种设备构件的内部,常常存在着不易发现的缺陷;如焊缝中的未熔合、未焊透、夹渣、气孔、裂纹等。要想知道这些缺陷的位置、大小、性质,对每一台设备进行破坏性检查是不可能的,为此出现了无损探伤法,它是在不损伤被检工件的情况下,利用材料和材料中缺陷所具有的物理特性探查其内部是否存在缺陷的方法。
应用无损检测技术通常是为了达到4个目的:保证产品质量、保障安全使用、改进制造工艺、降低生产成本。
1.射线检测
(1)射线检测原理。射线照射在工件上,透射后的射线强度根据物质的种类、厚度和密度而变化,利用射线的照相作用、荧光作用等特性,将这个变化记录在胶片上,经显影后形成底片的黑度变化,根据底片黑度的变化可了解工件内部结构状态,达到检查出缺陷的目的。
(2)射线检测的特点。可以获得缺陷直观图像,定性准确,对长度、宽度尺寸的定量也较准确;检测结果有直接记录,可以长期保存;对体积型缺陷(气孔、夹渣类)检出率高,对面积性缺陷(裂纹、未熔合类)如果照相角度不适当容易漏检;适宜检验厚度较薄的工件,不适宜检验较厚的工件;适宜检验对接焊缝,不适宜检验角焊缝以及板材、棒材和锻件等;对缺陷在工件中厚度方向的位置、尺寸(高度)的确定较困难;检测成本高、速度慢;射线对人体有害。
(3)射线的安全防护。射线的安全防护主要是采用时间防护、距离防护和屏蔽防护三大技术。
时间防护即为尽量缩短人体与射线接触的时间。如果到射线源的距离增大2倍,射线的强度会降低3/4.利用这一原理,可以采用机械手、远距射线源操作等方法进行距离防护。还可在人体与射线源之间隔上一层屏蔽物,以阻挡射线,即进行屏蔽防护。
2.超声波检测
(1)超声波检测原理。超声波是一种超出人听觉范围的高频率机械振动波。超声波可以分为纵波、横波、表面波等多种波型。当介质中质点的位移与波传播的方向一致时为纵波;质点的位移与波传播的方向垂直时为横波;而表面波只能在工件表面传播。在固体中,各类声波都可以传播;在液体和气体中,只有纵波才可以传播。超声波在同一均匀介质中传播时速度不变,传播方向也不变,如果传播过程中遇到另一种介质,就会发生反射、折射或绕射的现象。制造容器使用的钢材可视为均匀介质,如果内部存在缺陷,则缺陷会使超声波产生反射现象,根据反射波幅的大小、方位,就能判定和测出缺陷的存在。
(2)超声波检测特点。超声波检测对面积性缺陷的检出率较高,而对体积型缺陷检出率较低;适宜检验厚度较大的工件;适用于检测各种试件,包括检测对接焊缝、角焊缝,板材、管材、棒材、锻件以及复合材料等;检验成本低、速度快,检测仪器体积小、重量轻,现场使用方便;检测结果无直接见证记录;对缺陷在工件厚度方向上定位较准确;材质、晶粒度对检测有影响。
3.磁粉检测
(1)磁粉检测原理。铁磁性材料被磁化后,其内部产生很强的磁感应强度,磁力线密度增大几百倍到几千倍,如果材料中存在不连续,磁力线会发生畸变,部分磁力线有可能逸出材料表面,从空间穿过,形成漏磁场。因空气的磁导率远低于零件的磁导率,使磁力线受阻,一部分磁力线挤到缺陷的底部,一部分穿过裂纹,一部分排挤出工件的表面后再进入工件。这后两部分磁力线形成磁性较强的漏磁场。如果这时在工件上撒上磁粉,漏磁场就会吸附磁粉,形成与缺陷形状相近的磁粉堆积(称这种堆积为磁痕),从而显示缺陷。当裂纹方向平行于磁力线的传播方向时,磁力线的传播不会受到影响,这时缺陷也不可能检出。
(2)磁粉检测特点。适宜铁磁材料探伤,不能用于非铁磁材料;可以检出表面和近表面缺陷,不能用于检测内部缺陷;检测灵敏度很高,可以发现极细小的裂纹以及其他缺陷;检测成本很低,速度快;工件的形状和尺寸有时因难以磁化而对探伤有影响。
4.渗透检测
(1)渗透检测原理。零件表面被施涂含有荧光染料或着色染料的渗透液后,在毛细管作用下,经过一定的时间,渗透液可以渗进表面开口的缺陷中;除去零件表面多余渗透液后,再在零件表面施涂显像剂,同样在毛细管的作用下,显像剂将吸引缺陷中保留的渗透液,渗透液渗到显像剂中,在一定的光源下,缺陷中的渗透液痕迹被显示,从而探出缺陷的形貌及分布状态。
(2)渗透检测特点。除了疏松多孔性材料外任何种类的材料,如钢铁材料、有色金属、陶瓷材料和塑料等材料的表面开口缺陷都可用渗透检测;形状复杂的部件也可用渗透检测,并一次操作就可大致做到全面检测;同时存在几个方向的缺陷时,用一次操作就可完成检测;形状复杂的缺陷也可容易地观察显示的痕迹;不需大型设备,携带式喷灌着色渗透检测不需水、电,十分方便现场检测;试件表面粗糙度对检测结果影响大,探伤结果往往易受操作人员技术水平影响;可以检出表面张口的缺陷,但对埋藏缺陷或闭口型的表面缺陷无法检出;检测程序多,速度慢,检测灵敏度较磁粉低;材料较贵,成本高,有些材料易燃、有毒。
5.涡流检测
(1)涡流检测原理。在工件中的涡流方向与给试件加交流电磁场的线圈(称为初级线圈或激励线圈)的电流方向相反;而涡流产生的交流磁场又使得激励线圈中的电流增加,假如涡流变化,这个增加的部分(反作用电流)也变化,测定这个变化,可得到工件表面的信息。
(2)涡流检测的特点。检测时与工件不接触,所以检测速度很快,易于实现自动化检测;涡流检测不仅可以探伤,而且可以揭示工件尺寸变化和材料特性,例如电导率和磁导率的变化,利用这个特点可综合评价容器消除应力热处理的效果,检测材料的质量以及测量尺寸;受集肤效应的限制,很难发现工件深处的缺陷;缺陷的类型、位置、形状不易估计,需辅以其他无损检测的方法来进行缺陷的定位和定性;不能用于绝缘材料的检测。
6.声发射探伤法
(1)声发射探伤法原理。声发射技术是根据容器受力时材料内部发出的应力波判断容器内部结构损伤程度的一种新的无损检测方法。
(2)声发射探伤特点。它与X射线、超声波等常规检测方法的主要区别在于声发射技术是一种动态无损检测方法。它能连续监视容器内部缺陷发展的全过程。
7.磁记忆检测
磁记忆检测原理是处于地磁环境下的铁制工件受工作载荷的作用,其内部会发生具有磁致伸缩性质的磁畴组织定向的和不可逆转的重新取向,并在应力与变形集中区形成最大的漏磁场的变化。这种磁状态的不可逆变化在工作载荷消除后继续保留。从而通过漏磁场法向分量的测定,可以准确地推断工件的应力集中区。
(三)测厚
厚度测量是承压类特种设备检验中常见的检测项目。由于容器是闭合的壳体,测厚只能从一面进行,所以需要采用特殊的物理方法,最常用的是超声波。
(四)化学成分分析
钢铁材料元素分析的方法有原子发射光谱分析法和化学分析法两种。在用锅炉压力容器检验中进行化学成分分析的目的,主要在于复核和验证材料的元素含量是否符合材料的技术标准,或者在焊接或返修补焊时借此制定焊接工艺,或者用于鉴定在用锅炉压力容器壳体材质在运行一段时间后是否发生变化。
(五)金相检验
金相检验的目的主要是为了检查设备运行后受温度、介质和应力等因素的影响,其材质的金相组织是否发生了变化,是否存在裂纹、锅烧、疏松、夹渣、气孔、未焊透等缺陷。
金相检验分为宏观金相和微观金相,折断面检查是宏观金相检验方法之一。
金相检验可以观察到设备的局部金相组织。对于材料的金相检验,根据有关标准,可以判定钢材脱碳层深度,测定低碳钢的游离渗碳体,亚共析钢的带状组织和魏式组织,以及晶粒度等。对于在用压力容器金相检验结果的判定,目前尚无标准可循,通常可采用与典型缺陷金相图谱对比的方法来进行判定。在用压力容器的断口金相检验,还可以帮助我们判定腐蚀、断裂的类型,分析造成容器失效的原因。
(六)硬度测试
材料硬度值与强度存在一定的比例关系,材料化学成分中,大多数合金元素都会使材料的硬度升高,其中碳的影响最直接,材料中含碳量越大,其硬度越高,因此硬度测试有时用来判断材料强度等级或鉴别材质;材料中不同金属组织具有不同的硬度,故通过硬度值可大致了解材料的金相组织,以及材料在加工过程中的组织变化和热处理效果;加工残余应力和焊接残余应力的存在对材料的硬度也会产生影响,加工残余应力和焊接残余应力值越大,硬度越高。
(七)断口分析
断口分析是指人们通过肉眼或使用仪器观察与分析金属材料或金属构件损坏后的断裂截面,来探讨与材料或构件损坏有关的各种问题的一种技术。
断口是构件破坏后两个偶合断裂截面的通称。人们通过对断口形态的观察、研究和分析,去寻求断裂的起因、断裂方式、断裂性质、断裂机制、断裂韧性以及裂纹扩展速率等各种断裂基本问题,以使人们正确地判断引起断裂的真实原因究竟是起源于材料质量、构件的制造工艺、构件使用的环境因素影响,还是构件使用的操作因素等等。
断口分析技术的发展概括起来经历了3个阶段:用肉眼、低倍率放大镜或光学显微镜直接观察阶段,用透射电子显微镜(简称“透射电镜”)观察断口复型的间接阶段;用扫描电子显微镜(简称“扫描电镜”)直接观察阶段。通常人们把第一阶段称为宏观断口分析,而把后两个阶段称为微观断口分析,有时又称作“电子断口学分析”或“电子显微断口学分析”。
(八)耐压试验
承压类特种设备的耐压试验即通常所说的液压试验(水压试验)和气压试验,是一种验证性的综合检验,它不仅是产品竣工验收时必须进行的试验项目,也是定期进行容器全面检验的主要检验项目。耐压试验主要用于检验压力容器承受静压强度的能力。
(九)气密试验
气密试验又称为致密性试验或泄漏试验,当介质毒性程度为极度、高度危害或设计上不允许有微量泄漏的压力容器,必须进行气密试验。气密性试验应在液压试验合格后进行。对碳素钢和低合金钢制压力容器,其试验用气体的温度应不低于5C°,其他材料制压力容器按设计图样规定。气密性试验所用气体,应符合气压试验的规定。压力容器进行气密性试验时,安全附件应安装齐全。
容器致密性的检查方法:在被检查的部位涂(喷)刷肥皂水,检查肥皂水是否鼓泡;检查试验系统和容器上装设的压力表,其指示是否下降;在试验介质中加人体积分数为1%的氨气,将被检查部位表面用5%硝酸汞溶液浸过的纸带覆盖,如果有不致密的地方,氨气就会透过而使纸带的相应部位形成黑色的痕迹。用此法检查容器致密性较为灵敏、方便;在试验介质中充入氦气,如果有不致密的地方,就可利用氦气检漏仪在被检查部位表面检测出氦气。目前的氦气检漏仪可以发现气体中含有千万分之一的氦气存在,相当于在标准状态下漏氦气率为1 cm3/a,因此,其灵敏度较高;小型容器可浸入水中检查,被检部位在水面下约20—40 mm深处,检查是否有气泡逸出。
(十)爆破试验
爆破试验是对压力容器的设计与制造质量,以及其安全性和经济性进行综合考核的一项破坏性验证试验,通常气瓶在制造过程中按批进行爆破试验。
(十一)力学性能试验
力学性能试验的目的是检测材料及焊接接头的力学性能。检测方法有拉力试验、弯曲试验、常温和低温冲击试验、压扁试验等。检测的力学性能有比例极限σp、弹性极限σe、屈服极限σs、抗拉强度σb、伸长率δ5、断面收缩率Ψ、弯曲、冲击功Akv等。
(十二)应力应变测试
应力应变测试目的是测出构件受载后表面的或内部各点的真实应力状态。实验应力应变测试的方法主要有电阻应变测量法(简称“电测法”)、光弹性方法、应变脆性涂层法和密栅云纹法等,每种测试方法都有各自的特点和适用范围。
电测法是将作为传感元件的电阻应变片粘贴或安装在被测的承压设备表面上,然后将其接入测量电路,当设备受载变形时,应变片的敏感栅相应变形并将应变转换成电阻改变量,再通过电阻应变仪直接得到所测量的应变值。根据应力与应变关系的物理方程,即可将测得的应变值换算成被测点的实际应力值。用电测法可以进行大规模的多点应变测量,准确测定承压设备构件表面上任一点的静态到500 kHz的动态应变,还可测得平面应力状态下某些点的主应力大小和方向。但是,此法只能测试承压设备表面的应力,不能显示容器表面整体应力场中应力梯度的情况。
(十三)应力分析
应力分析是指分析构件在载荷的作用下,各应力分量。如分析一次总体薄膜应力、一次局部薄膜应力、一次弯曲应力、二次应力、峰值应力等。
(十四)断裂力学分析
断裂力学分析是应用断裂理论,对含缺陷构件的剩余强度和寿命进行分析的方法。断裂力学的观点认为,带裂纹的构件,只要裂纹扩展未达到临界尺寸,仍可使用。
(十五)风险评估
风险评价技术就是将设备发生事故的可能性(概率)和事故造成的危害程度(经济损失)进行综合考虑,将设备划分成不同的风险等级。
【例题】: 以下有关无损检测的说法正确的是:___。( )
A. 射线检测的特点,对面积性缺陷的检出率较高,而对体积型缺陷检出率较低;适宜检验厚度较大的工件;适用于检测各种试件,检验成本低、速度快。
B. 超声波检测特点,对体积型缺陷(气孔、夹渣类)检出率高,对面积性缺陷(裂纹、未熔合类)容易漏检;适宜检验厚度较薄的工件。
C. 磁粉检测特点,适宜铁磁材料探伤,不能用于非铁磁材料;可以检出表面和近表面缺陷,不能用于检测内部缺陷;检测灵敏度很高;检测成本很低,速度快。
D. 渗透检测特点,可以检出表面张口的缺陷,但对埋藏缺陷或闭口型的表面缺陷无法检出;检测程序多,速度慢,检测灵敏度较低;材料较贵,成本高,有些材料易燃、有毒。
E. 涡流检测的特点,不仅可以探伤,而且可以揭示工件尺寸变化和材料特性,检测速度很快,很难发现工件深处的缺陷。
【答案】:CDE
特种设备用钢材及焊接基础知识
(一)承压类特种设备用钢
无论是锅炉,还是压力容器,或是压力管道,钢材是制造承压类特种设备的主要材料。钢材的质量及性能的好坏对于承压类特种设备安全运行,有着重要的影响和作用。
1.按钢中所含化学成分分类
按钢中所含化学成分可以将钢分成碳素钢和合金钢两大类:
2.按冶炼方法分类
按冶炼方法分类,有两种形式,一种是按冶炼设备分为平炉钢、电炉钢、转炉钢;另一种是按脱氧程度分为镇静钢、沸腾钢、半镇静钢。
3. 按金相组织分类
钢材经正火处理后所得金相组织不同,可分为珠光体钢、贝氏体钢、奥氏体钢、铁索体钢。
(二)金属的机械性能
所谓金属的机械性能是指在一定的温度条件和外力作用下,抵抗变形和断裂的能力,如强度、硬度、塑性、韧性等,也称力学性能。
以低碳钢为例,金属材料受拉伸外力作用引起的变形过程可分3个阶段,即弹性变形、塑性变形、断裂变形阶段。由拉伸试验可获得强度和塑性指标。
1.强度
金属强度是指在外力作用下,抵抗变形和破坏的能力。应用最普遍的是强度指标。强度指标主要是屈服极限(σs或σ0.2)和抗拉强度极限(σb)。
2.塑性
金属的塑性是指在外力作用下,能引起永久变形而不发生破裂,并在外力取消后,仍能保持变形后形状的能力。材料的塑性值也可通过拉伸试验测得,通常用伸长率δ(延伸率)和断面收缩率Ψ来表示。
3.冲击韧性
金属的冲击韧性即为在冲击力作用下,抑制变形和断裂的能力。它还是金属材料在塑性变形范围内吸收能量的能力,因此,也可按冲击值的大小来衡量材料的塑性。目前国内外广泛采用一次摆锤弯曲试验,缺口型式有夏比(U)和夏比(V)两种。表示冲击韧性的参数也有两种,一种是以冲断试样消耗的冲击功Ak,单位是焦耳(J);另一种是以单位缺口处断面所耗的冲击功ak,单位是焦耳/厘米2(J/c㎡)表示。目前压力容器钢板全部改为用夏比(V)冲击功(即Akv)作为冲击韧性验收标准。只有少数压力容器锻件还用夏比(U)冲击值(即akU)作为冲击验收标准。
钢中气体含量较高或晶粒粗大,则韧性差。根据冲击后断裂的形式,可以判断材料的质量及晶粒大小。冲击韧性试验还能测定金属材料由韧性状态向脆性状态过渡的转变温度。
4.硬度
硬度是指金属材料抵抗更硬异物压入的能力。硬度表明材料的耐磨性和切削加工的可能性。一般说来,硬度较高,材料的耐磨性较好。常用的硬度有布氏硬度(HB)洛氏硬度(HR)维氏硬度(HV)3种。
5.冷弯
冷弯性能是材料抵抗弯曲断裂能力的标志,它间接反映了材料的塑性。这个试验既可检查钢的塑性好坏,也可以考核其加工工艺性能,也能暴露钢板受试面缺陷以及焊接接头的焊接缺陷。
6.断裂韧性
断裂韧性是反映材料对裂纹扩展的抵制能力。对于中低强度钢的断裂韧性,目前较普遍采用临界裂纹张开位移(COD)值δc表示;对于高强钢的脆断问题,则应用材料的平面应变断裂韧性值Kic表示。
7.金属材料高温机械性能
炼油化工设备相当数量是在中等温度(<350℃)和高温下使用。中、高温压力容器通常以350℃分界。
责任编辑:棋雯
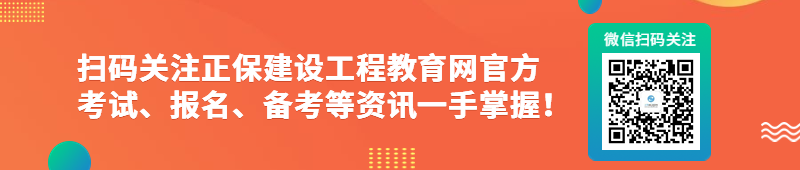